
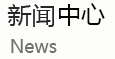
探秘 | 西门子在华首个数字化工厂,“混线生产”把我惊呆了!【视频】
发布时间:2015-03-04
据新华网消息:2月21日,德国总理默克尔在联邦政府播客中说:德国工业产值占国内生产总值的20%,德国希望继续保持工业强国地位,数字化生产对德国的繁荣富裕至关重要。德国工业生产必须迈向数字化,即实现“工业4.0”,而如今已是时候设立相关标准。
默克尔说:“德国可以成为特定标准的推动者,并使其扎根欧洲,同时我们也有机会将其推向全球。”
“数字化工厂”到底如何落地?西门子成都基地无疑成了我们了解德国工业4.0最便捷的窗口。
视频 西门子在华首个数字化工厂
在工业4.0的时代图景下,制造业正在发生一场怎样的变革?作为制造业基础组织单元的“工厂”,将会迎来一次怎样的颠覆?
变革的时代,新鲜的概念、前沿的理念层出不穷。而一个有说服力、有参照价值的样本,或许能给身处变革大潮之中的企业带来更多鲜活的印象与具象的感触。
在成都市西北角,距离郫县县区3公里处,坐落着一座看似普通的“特殊工厂”。这座正式投产仅一年多的工厂内,设置了一个由各种系统组合而成的全集成自动化流程展示图。展示图中,工厂的处理系统相当于大脑,连接网络如同它的神经,驱动系统就像是肌肉,传感器就相当于眼睛和鼻子。事实上,这个仿如人体系统一样的工厂内,“数据”是从研发到生产到管理和配送,每个环节机器间沟通的“语言”。
这样一座以数字化为中心,通过自动化设备和各种软件互联互通的工厂,正是西门子在中国设立的首家数字化工厂——西门子工业自动化产品成都生产研发基地。
近日,带着为“智能制造”寻找样本、为“车间进化”探访案例的意图,《南方日报》记者前往成都,实地揭秘这座短短一年内就接待了4000名考察访客的前沿工厂。
驱动系统是肌肉,传感系统是眼鼻,自动化工厂“被想象成人体”
西门子成都数字工厂在投产后意外地成为了“景点”,甚至EMBA课程也把它列入其中当成一个案例研究。这座强调“数字化”的工厂,首先是一个实现了全集成自动化的“人体”,相比同类型普通工厂节省人员近50%,最大程度实现自动化的物流配送。这不仅节省了占地和劳动力,还如同一个“聪明的小护士”,知道什么时候要给“医生”(工厂)递怎样的“手术刀”(物料)。
当迎来一个又一个的参观者时,西门子也感到有些意外。
这座占地35300平方米,外形与普通工厂无异,被西门子命名为“工业自动化产品成都生产研发基地”(以下简称“SEWC”)的全新工厂,在一年半前正式投产运营。对外开放后,这座由西门子在中国设立的首家,也是唯一一家数字工厂,意外地成为成都高新区内一个新“景点”。
“从2013年9月正式运营起,一年内相继来参观的人就达到4000人。”西门子工业自动化产品成都生产研发基地卓越运营部经理戴霁明对南方日报记者表示,这些慕名而来的访客来自美国、以色列、中国等,包括官员、企业家、客户等,甚至一些大学也把SEWC列入EMBA课程的一个研究案例。
事实上,作为西门子在全球建立的首家数字工厂,德国安贝格工厂建于25年前(太超前了!)。但仅用一年多的时间,位于成都的SEWC的生产质量就已与德国安贝格工厂看齐。目前SEWC的产品合格率达到99.85%。“以投产一年多的时间来看,这是非常好的成绩。”西门子工业自动化产品成都生产研发基地副总经理李永利说。
如同SEWC的命名,数字化工厂是一座强调“数字化”的“机体系统”,它首先实现了全集成的自动化。
“我们把自动化后的工厂想象成人体。”戴霁明说。在SEWC参观走廊上,一个被称为全集成自动化的展示板中,贴满了各种各样的工业系统,但这些系统却各自拥有“特殊”的名称。
在这座到处都是传感器的工厂里,戴霁明指着展示板说道,工厂的处理系统就相当于大脑,连接下面的网络就是它的神经,驱动系统就是肌肉,传感器就相当于眼睛和鼻子,这样形成一个像人一样自动运转的整体。
基于全集成自动化,在SEWC参观走廊的下方,仅占用工厂1/10占地面积的生产车间内,并没有普通工厂常见的传统的物料暂存区。“所有产品完成生产后直接由产线发出,进入物流中心进行配送。”戴霁明说。
从整个生产工序来看,工厂从自动取料开始,先进行印刷电路板的工段,之后进行贴片、穿孔等全部已经实现自动化的生产工序,再统一送到车间中转库,由其进行生产线分配后再组装。
在这样的产线上,只有几名工人不时看着屏幕上的数字化看板。看板上,红、黄、绿三种颜色代表着物料的数量。每当物料经过工人座位上的扫描枪,就会实现自动扫描,若物料出现短缺,就会马上传送到自动物流仓库。
这个被称为自动物流系统的部门,走到原材料的存放处,是两个高达18米的自动化高位货架,两部高速运转的取料机如同人一样。根据后台的数据提示,这两部取料机依靠数字定位迅速地抽出对应的原材料,并通过自动传输轴,马上传送到生产车间。
“当物料需求的信息传导到自动物流仓库,仓库最长只需要30分钟就能把物料送到车间。”戴霁明表示,这套自动化系统不仅替代了大量的员工,而且还可以实现小批量多批次的发货。“整套系统就像聪明的护士,它知道医生(工厂)什么时候需要它传递什么样的手术刀(物料)。”
而这样一个管理着2万多个箱子的物流部门,仅有12个人。按照传统工厂的“三班倒”,这意味着每一个生产班次中仅有4名员工负责管理物流仓储。
事实上,来自SEWC提供的情况显示,在该工厂内仅有350人,其中生产车间员工仅100人。“以平均水平来看,数字化工厂的人员相比传统工厂节省30%到50%的人员。”李永利说。
“数据”成机器之间的“语言”,近百款软件实现互联式沟通
与普通的工厂相比,SEWC在使用ERP、PLM等软件时,最大不同是实现了所有软件的互联互通,以及虚拟和现实的交互。这是追随者要学习攻克的难点,也是迈向工业4.0的关键点。而同样借助软件,在SEWC中进行的所有研发都靠“电脑”完成,只有在最终生产时才“落地”变现。
但所谓数字化工厂,并不仅仅停留在通过全集成自动化来减少产线上的蓝领员工。李永利表示,数字工厂内借助大量不同的软件,以此实现对于部分“白领”群体的“替代”,即企业生产管理层面的效率提升。
“我们工厂内正在使用的软件至少有数十到近百类。”戴霁明说,这些软件的单个或多个使用在国内其实很普遍,比如ERP、SAP等。“但数字化工厂与传统工厂最大的不同是,我们所有软件之间的数据都实现了打通,系统之间实现了互联互通。”
而要实现不同软件、系统之间的互联互通既是最大的难点,也是数字工厂迈向工业4.0的重要一点。正如在乌尔里希·森德勒主编的《工业4.0——即将来袭的第四次工业革命》中提到的,“软件是工业的未来”,并强调“通过软件的交互性并不仅仅是在生产层面,还在于业务层面”,也就是说,“通过工业软件,实现了虚拟和现实的交互。”
在SEWC内部,要让数据成为机器之间沟通的“语言”,其中重要的一点是,采用拥有彷如“中枢神经”一样的“数据管家”,即Teamcenter。通过这个“管家”,工厂内不同的软件、系统和部门都可以实时摘取数据,或实时导入数据。
在SEWC三楼的工厂参观走廊上,一个工业显示屏上实时地显示着工厂内部不同环节的数据。戴霁明用手指点击屏幕上的“工厂原材料配送实时情况”一栏,“你看,屏幕里显示有一块物料刚出仓。再过一会儿,它马上就被送到车间来了。”
各类软件的互联后,数据实现了交互,也让整个工厂的运转变得更有效率。
李永利举例,比如有一款产品的元器件发生了变化,首先Teamcenter会释放这一数据给财务系统中的SAP软件,以此更改原材料。随之如果可能发生价格变化的话,采购系统也会自动更新。
基于元器件的变化,到了制造环节,涉及到原材料的使用就存在两个版本。李永利表示,借助MES软件,产线就能自动了解到什么时候应该用哪一种元器件,生产哪一个版本。而MES软件的数据统一是来自于Teamcenter。
简而言之,在SEWC工厂内,一旦产品数据发生变化,只要研发人员和制造人员在Teamcenter中进行数据更改,之后的制作流程就会自动传到MES,MES会根据新的制造解决方案分配产线和时间,“到时候一样可以计算出,工人到几点几分会生产什么产品,因为MES能精确计算出每件产品的耗时。”李永利说。
当这些工作都不再通过具体的人去沟通后,工厂的生产管理效率自然大大得到提高。
而同样是借助软件,工厂的研发也实现了“数字化”。一般的工厂在进行研发时,从定义产品时涉及的市场分析,开发产品时大量的分工讨论,乃至到最后生产产品时生产线的设计和调试,往往周期长,投入大。但在SEWC内,工厂却是通过借助软件和3D打印,大大缩短了产品的研发周期。
SEWC里一块名为NX计算机辅助系统的屏幕上,展示了这一过程。“我们会先做出一个虚拟的样机。”戴霁明表示,在软件的支持下,虚拟的样机能够模拟包括如力学、热力学等电器性能,在完成测试后,工厂再用3D打印等方式做模具。
“以前改模一般都需要5到6次以上,但现在缩短到只需要1到2次。”他说。
而到了生产线设计和调试时,同样通过仿真软件,只要把各种数据输入软件,以此模拟生产线,只要看着系统的运转,就能马上看出要如何做调试——【注:西门子的“可见即可得”理念】
也就是说,工厂的研发几乎都在“电脑”中进行。而唯有最终确定生产线设计方案后,才真正“落地”变现。
“混线生产”应对小批量定制,出现质量问题会“自我举报”
细心观察SEWC的生产线,会发现一条产线上同时生产多款产品。利用交替生产的方式,SEWC首先保证不同批量的产品实现交货期稳定,同时让特殊的系统成为产线上的“导游”,指引不同产品的生产,甚至在产品“堵车”时管制“交通”。而一切的数据互联,最终还能让工厂实现自我的质量监控,以此实现数字化工厂“质量第一”的目标愿景。
当“数字”成为了SEWC内不同部门、不同系统之间沟通交流的“语言”,成为如同一个生命有机体的“血液”后,数字化制造并不仅仅体现在提高生产效率,它还体现在对“柔性化生产”、“智能制造”的探索和实现。
在SEWC的生产线上,如果细心地去看,会发现同一条产线轴上正在运载的产品并非同一的产品。
“这是未来制造中常提到的‘柔性化生产’,我们在具体运作中,叫混线生产。”戴霁明表示,一般情况下,工厂接到的订单往往是十分零散,且订货数量和交货周期都不同。在这种情况下,按照普通工厂“专线专用”的方式,如果是大批量的产品,每次生产同样的产品,且物流准备和工人操作也比较熟练,生产线的效率自然会比较高。但一旦涉及到多个小批量订单,就可能会出现小批量订单交货周期不稳定且偏长的问题。
“为此,我们把大单拆成小单,交替生产,这样大家得到的交货期就是稳定的。”戴霁明说道,但要实现一条生产线上同时生产不同类型的产品,就很容易出错。
这种既要实现混线生产,又要避免出错,西门子成都数字工厂如何实现?答案是借助MES系统,充当产线上的“导游”。
为使用MES系统来管理混线订单,工厂在产线上密布很多传感器。每当有一个配件经过特定的地方,就会由RFID进行识别,之后MES系统就会对这个配件发出“指令”,“告诉”它接下来应该走怎样的线路,而这个配件所走过的所有的路线,和经过的工序也会传达到MES系统中。如果“导游”发现路线没有错,确认过后,产品就会被送到包装终站,最后完成这趟“旅程”。
有意思的是,在整个生产系统中,一旦“旅程”中出现“拥挤”或者有其他问题出现,系统就会自动地锁定。
“这种做法在汽车行业目前也有采用,但SEWC的混线生产中,产品的流转节拍可以发生不同。”戴霁明进一步解释道,也就是说,一旦产线上前面的产品出现“堵车”,就会看到后面的产品自动停下来“等待”。
而大量传感器的应用也把产线上的各种数据实时传导到像中枢神经系统一样的Teamcenter之中。
当整个工厂内部如同一个“人体”运转时,就连工厂的运转也变得“透明”起来,一旦工厂内出现质量问题,机器还能实现“自我举报”。
伴随密布工厂的传感器实时把生产信息传导到MES系统中,系统在进行质量管理后会把信息显示出来。“数字化系统把质量信息实时同步展示的时候,连客户也能随时看到,实现了质量信息的透明化。”戴霁明说。
“数据”连接起了各种管理系统,如同数字化工厂内的神经、脉络都被打通,并由此流动起来。一旦有显示质量问题的数据出现,系统实时监测到后,就会立刻自动发送邮件给相关的人和部门,而这些情况,在后台系统上也能够全部看到。
戴霁明表示,普通的工厂一般都缺乏这样的质量管理体系,质量报告往往是隔一天甚至更长的时间才发出,而当你发现这个质量缺陷时,一大批的次品可能已经发出去。
为此,正如李永利在接受采访时反复强调的:“数字化工厂的建立,最终不是为了降低成本,而是为了追求更高的质量。”
■数读
4000人 从2013年9月正式运营起,SEWC在第一个财年内迎来参观人数达到4000人。除了有来自美国、以色列、中国等各地慕名而来的官员、企业家、客户等之外,甚至还有一些大学也将SEWC列入EMBA的学习课程。
50% 以平均水平来看,数字化工厂的人员相比传统工厂节省30%到50%。比如像SEWC工厂内一个管理着2万多个箱子的物流部门,仅有12个人,按照工厂“三班倒”,意味着每一个生产班次中仅有4名员工负责管理物流仓储。
近百类 SEWC工厂内正在使用的软件至少有近百类,数字工厂与传统工厂最大的不同是,工厂所有软件之间的数据都实现了打通,系统之间实现了互联互通。
1次 实现了研发“数字化”的SEWC工厂,以前改模一般都需要5到6次以上,但现在缩短到只需要1到2次。
■解读
“语言” 在西门子成都数字工厂中,“数据”是从研发到生产到管理和配送,每个环节机器间沟通的“语言”。
“人体” 工厂的处理系统就相当于大脑,连接网络如同它的神经,驱动系统就像是肌肉,传感器就相当于眼睛和鼻子。
“护士” 成都工厂的自动物流系统就像聪明的护士,它知道医生(工厂)什么时候,需要它传递什么样的手术刀(物料)。
“管家” 在成都工厂内部,要让数据成为机器之间沟通的“语言”,其中重要的一点是,采用拥有仿如“中枢神经”一样的“数据管家”,即Teamcenter。通过这个“管家”,工厂内不同的软件、系统和部门都可以实时摘取数据,或实时导入数据。
“导游” 在数字工厂的生产线上,同一条产线轴上正在运载的产品并非同一款的产品。在实现混线生产的产线上,MES就像是产线上的“导游”,对每一个配件发出“指令”,确认它所经过的所有路线。
转自:中国纺机 |
